Description
Task
Software limit switch monitoring (SLS monitoring) is used to monitor the command and actual positions of an axis. A positive SLS (P-AXIS-00178) and a negative SLS (P-AXIS-00177) can be configured for each axis.
The positions of the SLS are always referred to the axis coordinate system.
Condition
The monitored axis must be referenced (G74) or P-AXIS-00014 must be configured.
Effectiveness
This is why a distinction is made between SLS monitoring based on the command value or actual value.
- Command positions are checked for exact compliance with the SLS.
- A tolerance of the actual position is configured for monitoring overshoots of SLS using P-AXIS-00179. This prevents the output of an error message in the event of negligible overshoots.
Command position related software limit switch monitoring is executed during path preparation.
In certain applications, the command position of axes is influenced by circumstances (e.g. gear coupling) that are unknown when planning contours. In these cases, the parameters P-AXIS-00520 and P-AXIS-00521 can be used in the position controller to activate the monitoring of command position values.
The actual positions are always monitored in the position controller.
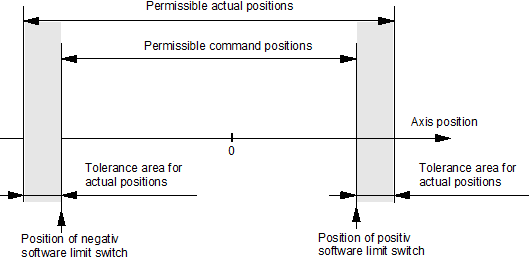
Activation
SLS monitoring of the command and actual positions of an axis is activated in all the operating modes available as soon as the axis is referenced.
As of Build V3.1.3037.11 the parameter P-AXIS-00705 can be used to switch on/off the SLS monitoring feature irrespective of axis type or axis mode.
Notice
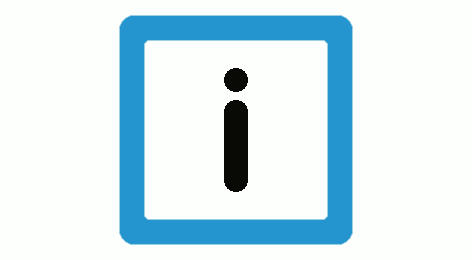
SLS monitoring of the command and actual positions is not active for rotary axes that were configured as modulo axes.
CAUTION
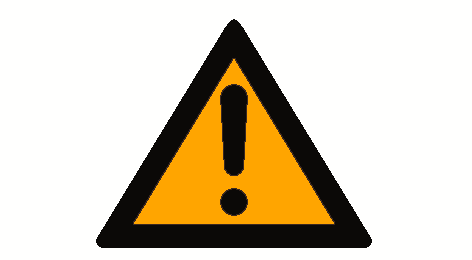
Incorrectly configured SLS positions may cause personal injury and machine damage
DANGER
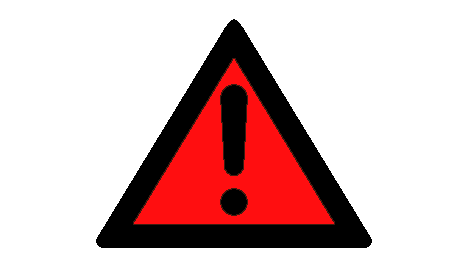
If axes are operated without software limit switches, the risk of personal injury and machine damage increases to a considerable extent.
Warnings, errors and reactions
Automatic mode and manual block, axis referenced
- Error message P-ERR-120002 or P-ERR-120003: A command position that overshoots an SLS is calculated by an NC block.
- Interpolation is stopped.
- The NC program is aborted at this NC block and the axes participating in the motion are stopped.
- The NC block is not executed; the nominal contour is not violated.
- Reset the controller.
- Error message P-ERR-70021 or P-ERR-70022: The actual value of the axis position overshoots an SLS.
- Interpolation is stopped.
- The affected axis is decelerated by a linear velocity profile. The nominal contour may be violated if several axes were involved in the motion.
- Reset the controller.
Manual mode (HB) with referenced axis (G200/G201)
- Warning P-ERR-50720: A software limit switch is reached in continuous jog mode. The warning is output only if P-MANU-00014 is configured accordingly.
- The motion is stopped.
- Move back within the valid range.
- Warning P-ERR-150008: In incremental jog mode, the step is no longer executed if it causes an overshoot of an SLS.
- The motion is stopped.
- Move back within the valid range.
Notice
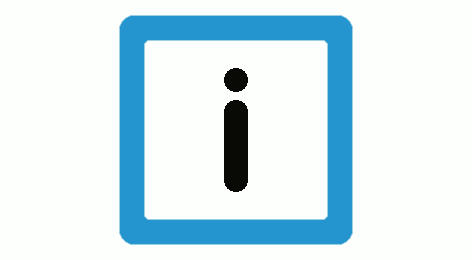
The possible motion range in manual mode can be limited by P-AXIS-00137 and P-AXIS-00138.
Manual mode (HB) with referenced axis (G200/G201)
Instead of the SLS, the HB offset limits (P-AXIS-00137 and P-AXIS-00138) are used.
- Warning P-ERR-50720: A HB offset limit is reached in continuous jog mode. The warning is output only if P-MANU-00014 is configured accordingly.
- The motion is stopped.
- Move back within the valid range.
- Warning P-ERR-150008: In incremental jog mode, the step is no longer executed if it causes an overshoot of an HB offset limit.
- The motion is stopped.
- Move back within the valid range.
CAUTION
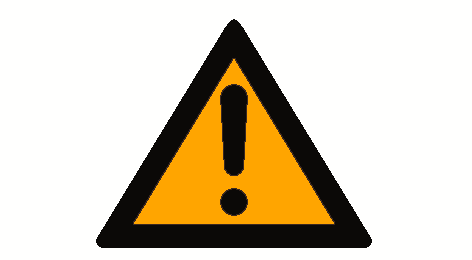
If offset limit monitoring is inactive, no range monitoring takes place. This may cause machine damage.