Programming
Syntax: |
#FILTER [ON | OFF] [ORDER=.. ORDER_TIME=.. SHARE=.. AX_DEV=.. FCUT=.. ACC_FACT=.. QUALITY=.. ] |
ON | Enable FIR filter. |
OFF | Disable FIR filter. |
ORDER=.. | Specify filter order |
ORDER_TIME=.. | Specify filter order over time in [µs] |
SHARE=.. | Define the degree of effectiveness (analogous to P-AXIS-00590) of the filter in [%] |
AX_DEV=.. | Specify the tolerance for tolerance monitoring in [mm, inch *]. |
FCUT=.. | Specify the cut-off frequency (analogous to (P-AXIS-00585) of the filter in [Hz] |
ACC_FACT=.. | Increase the path velocity at block transitions with FIR filter enabled. The greater the value setting, the less the velocity is reduced at the block transition. This requires a valid setting of P-AXIS-00013 (a_trans_weight) for the axes. Value range = 1.0 – 10.0 Default value =: 1.0 |
QUALITY=.. | Specify the filter quality of the filter core curve Parameter available as of V3.1.3075.04 |
Notice
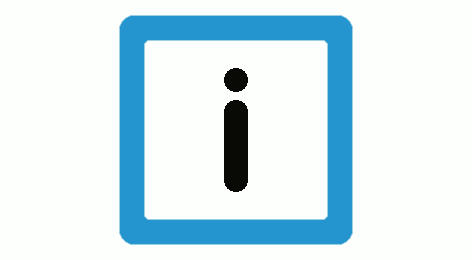
The #FILTER ON/OFF command enables or disables all the FIR filters of the axes in the channel.
It is possible to use FIR filters on all axes. It is also possible to use different filters for each axis by axis-specific configuration in the axis lists.
FIR filters can be globally enabled or disabled and reparameterised across all axes in the NC program during machining (see Programming example).
Notice
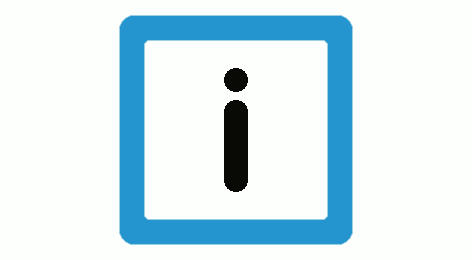
Tolerance monitoring can only be configured and activated in the NC program.
Tolerance monitoring is programmed by the parameter AX_DEV. It ensures that every axis remains within the specified tolerance [mm, inch].
Tolerance monitoring always monitors all axes and therefore can only be controlled globally in the NC program.
Tolerance monitoring in only active if AX_DEF was specified with a corresponding tolerance.
Programing Example
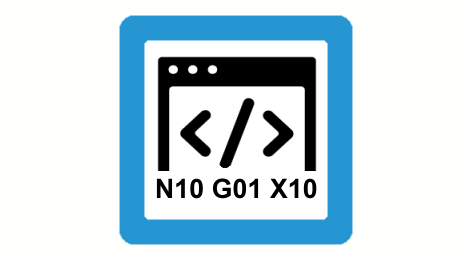
NC program with 90° corner
Program with a simple square contour. Traverse feed rate=4000mm/min, slope type=TRAPEZ (non-linear) and tolerance (AX_DEV)=0.001mm.
Setting in the axis lists:
- filter_fir.type 1
- filter_fir.order 40
The contour is traversed 3 times:
- first with filter and tolerance monitoring
- only with filter
- finally as reference without filter enabled.
N010 G00 G90 X0 Y0 Z0
N020 #SLOPE [TYPE=TRAPEZ]
(Contour with filter and tolerance monitoring)
N030 #FILTER ON [AX_DEV=0.001]
N040 G01 X0 Y1 F4000
N050 G01 X1 Y1
N060 G01 X1 Y0
N070 G01 X0 Y0
(Contour only with filter)
N080 #FILTER ON
N090 G01 X0 Y1 F4000
N100 G01 X1 Y1
N110 G01 X1 Y0
N120 G01 X0 Y0
(Contour without filter or tolerance monitoring)
N130 #FILTER OFF
N140 G01 X0 Y1 F4000
N150 G01 X1 Y1
N160 G01 X1 Y0
N170 G01 X0 Y0
N180 M30
Blue | without filter |
Red | with filter |
Green | with filter and tolerance monitoring |