Referencing
CNC-controlled
All gantry axes are referenced sequentially if homing is performed by the CNC. The homing logic is always executed for one axis and the remaining axes in the gantry combination are also interpolated uniformly. This is then repeated for the next axis in the gantry combination until all gantry axes are referenced.
During the homing motion, no relative motion of the gantry axes to one another occurs.
Drive-controlled
Intelligent drives (e.g. SERCOS) execute homing independently. In a gantry system, it must also be ensured that the gantry combination always moves uniformly. In other words,
- the parameter definitions must ensure that the drive covers an identical path during homing motion (RPF).
- The homing motion is started simultaneously for all gantry axes.
This behaviour is set by the parameter P-AXIS-00253.
Notice
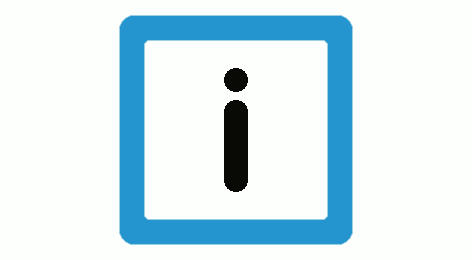
Drive-controlled reference point travel must run identically in the case of both drives (e.g. without cam and distance-coded measurement system). This must be initiated by respective parameters.
Attention
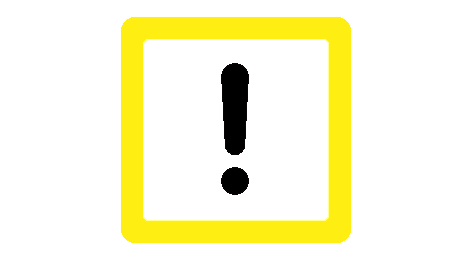
For security reasons the torque can be reduced during homing procedure.
Only on the master side
The parameter P-AXIS-00074 (gantry_slave_no_homing) can suppress homing for gantry slave axes.
When master axis homing is completed, the reference positions entered in the axis parameter list of slaves axes are adopted. Monitoring is started for the gantry difference between master and slave axes.
Monitoring before referencing
The parameter P-AXIS-00249 (gantry_diff_check_without_homing) is used to activate monitoring of the gantry difference between master and slave axes before homing is executed.
The offset between the master and slave axes at the time of controller start-up is used as the position offset.