Weighting factors for tool life and tool life distance ((V.TLM)
The NC program can change the weighting of service life values. Changeable factors are used to adapt tool life acquisition to tool use.
In the case of every tool change initiated by the T or D command (see P-CHAN-00482), the complete tool ID, the tool life time and the tool life distance are sent to the tool management system. All parameters are then zeroed and tool life acquisition is enabled for the new tool substituted.
The following two decoder variables are used to program the weighting factors of service life and service distance (access is not synchronous with real time):
Syntax: | |
V.TLM.TIME_FACT | Weighting factor of tool life time ≥ 0.0 |
V.TLM.DIST_FACT | Weighting factor of tool life distance ≥ 0.0 |
The variables can be read and written. The two factors are 1.0 (100%) at the first program start after controller start-up. Factors changed in the NC program are modal after program end and reset. As required, you must reset explicitly to 1.0 in the NC program but you can also programmed with values > 1.0 if this is necessary. Both variables may be written in an NC block.
Example
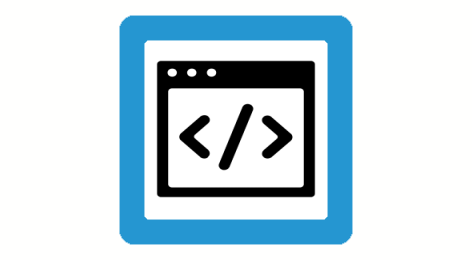
If a tool is always in contact, it should be weighted with a factor of 1.0 (100%). However, if material is only removed on half the motion path, a weighting factor of 0.5 may be included in the calculation. The default value of the weighting factors for service time and service distance is 1.0.
Capture conditions:
- Rapid traverse blocks are not included in tool life acquisition.
- Tool life acquisition is stopped at a feed rate of zero.
- With the exception of rapid traverse interpolation, all motion types are included in tool life acquisition. For example, G01, G02, G03, spline interpolation and G63 are included.
- The weighting factors are included in the calculation.
- A distinction is not made between main and tracking axes for axes participating in the motion. The path feed rate is always used to add up the distance. If tracking axes are programmed on their own in the block, the path covered by the tracking axis is added to the service distance. If this is not desired, the programmer can correct it by specifying the weighting factors V.TLM.TIME_FACT/DIST_FACT = 0.0.
- Active master/slave arrangements are not taken into account.
- In the case of a reset or program abort, the last current values are also saved to the database of the tool management system.
- If only substitution occurs, i.e. no tool was previously in the work spindle and the current T number is zero, no data is sent.
- Tool data is only sent if a tool management system is actually present (P-CHAN-00016).