Moved workpiece
The moved workpiece is a subfunction of kinematic 45. It allows the control of an industrial robot where the workpiece is attached to the flange by a standard processing program, whereas the (milling) tool has a fixed position in space.
Notice
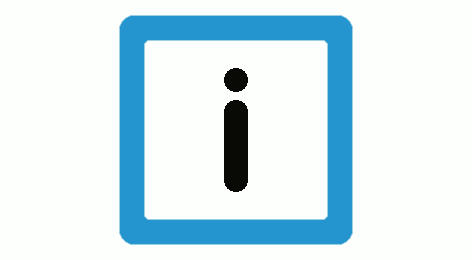
The further the robot is away from the fixed tool, the greater the movement of the robot when changing the orientation ABC.
This function is activated by the kinematic parameter HD33 of kinematic 45.
Tool set-up
The tool parameters for kinematic 45 can be directly entered in the parameters HD1-6 or they can be activated by a suitable tool by means of tool-head offsets when the tool is selected.
Tool-head offsets are added to the kinematic parameters (no concatenation takes place). If this function is used, it is recommended to set the parameters HD1-6 in the channel parameter list to “0”.
Parameterisation example of HD1-3 for a fixed tool:
Example: Parameterisation of HD4-6 for a fixed tool:
Tool set-up
Offsets of the coordinate system into the workpiece now have the robot flange system as the lowest reference point for the moved workpiece.
Every further offset/rotation haves as usual.
Only one tool can be active at any one time. This is the machining tool of the moved workpiece. A gripper on the flange can be defined by an offset (e.g. #CS).
The parameterisation example below refers to the standard flange orientation (HD 31 = 0).