"INDIRECT" mode
"INDIRECT" mode (P-AXIS-00753) can be used if the measuring system does not include the vibration to be damped (P-AXIS-00751). The mechanical vibration is simulated by a digital filter:
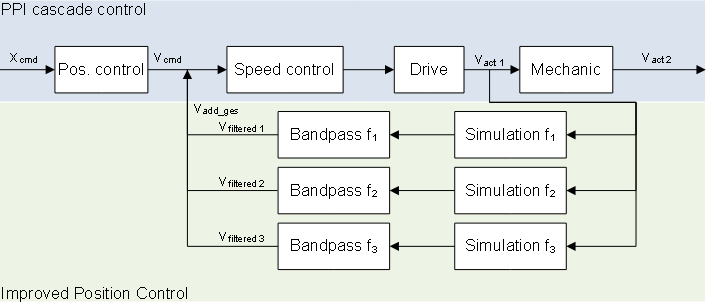
A simulation of the mechanical vibration can be executed by specifying a separate damping ratio (P-AXIS-00756) for each of the frequencies to be damped. The simulation results are handled in the same way as the results from measurements taken from a direct measuring system. The frequency range is reduced to the relevant frequency by using a suitable band-pass filter. After weighting the results, an additive speed is added to the manipulated variable causing a counter-motion of the motor to compensate for the vibration.
Advantage of "INDIRECT" mode
Compared to *DIRECT" mode, "INDIRECT" mode offers the advantage of producing strong excitation in the simulation, even for weak vibrations that are not visible in the motor actual values or from the direct measuring system. This allows the "Improved Position Control" function to damp vibrations that are not suitable for *DIRECT" mode.
Attention
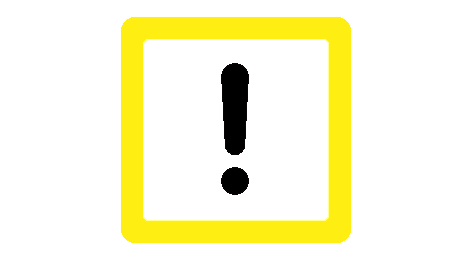
Excessive scaling of the additive speed may cause the motor to vibrate.
Consequence: The control loop becomes unstable.
Attention
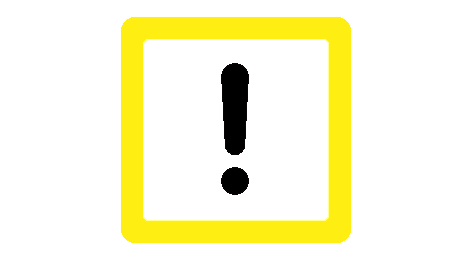
At high frequencies, a phase shift of the output additive speed may occur due to the dead time of the simulation.
Consequence: Vibrations may be intensified instead of being damped.
Attention
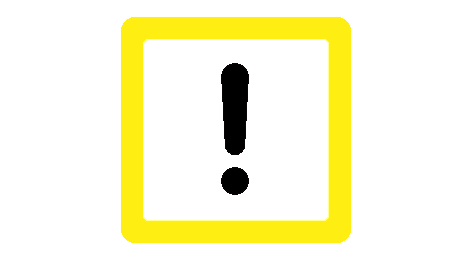
Low damping ratios may cause the output of high additive speeds.
Consequence: The drive may be excited to vibrate.