Introduction
Release Note
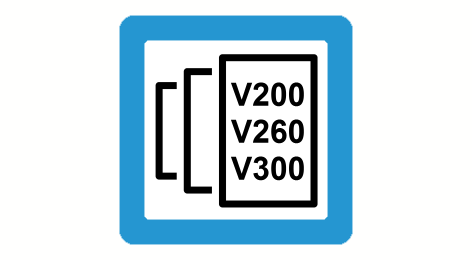
This function is available as of TwinCAT 3 and higher.
Definition of McCOM
Motion Control Component Object Model is a binary interface standard in machine tool controllers.
Based on the Microsoft COM standard, McCOM defines how various software components developed and generated independently can cooperate in real time.
The acronym TcCOM stands for the TwinCAT Component Object Model concept.
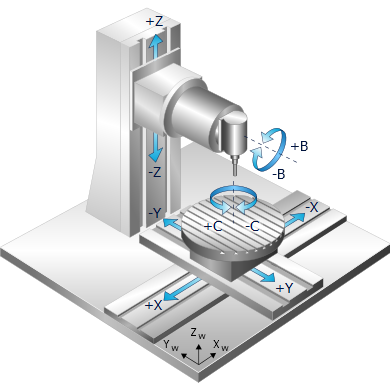
Kinematic structure
To simplify workpiece programming, the kinematic transformation encapsulates the machine’s kinematic structure and abstracts the motions in a simple Cartesian coordinate system.
Licensing note
Please note that the use of the transformation interface is an additional option and subject to the purchase of a license..
Forward/backward transformation Forward/backward transformation
Depending on the machines' kinematics, the CNC needs the transformation between axis coordinates and programming coordinates to calculate motions. With the aid of this kinematic transformation, the coordinates of the NC program (forward transformation, ACS -> MCS) are calculated from the physical positions of the axes. Conversely, backward transformation calculates the axis positions from the programmed NC positions (MCS -> ACS).
Selecting/deselecting
Transformation is selected by means of an NC command in the NC program, for example.

Extendibility
You can create a user-defined transformation and make it available to the CNC under a selected number (ID). The range [500; 999] is provided as the transformation numbers for this operation. The range [65; 69] continues to be provided for compatibility reasons.