Drives with position control in the drive
Parameterising the drive
Control with digital drives takes place in the drive itself. The CNC specifies a position/speed command value for the drive per tracing interval. The current actual value (position and speed) can be used in the CNC for display functions and monitoring.
In addition, the CNC sends the required operation mode cyclically to the drive.
SERCOS parameters
The following parameters are essential for a SERCOS drive for the position/speed control operation modes:
Main operation mode S-0-0032 = 3 (position actual value with encoder 1)
- S-0-0051 position actual value (encoder 1) / S-0-0053 position actual value (encoder 2)
- S-0-0047 position command value
Auxiliary operation mode 1 S-0-0033 = 2 (speed control)
- S-0-0040 speed value
- S-0-0036 speed command value
In addition to the auxiliary operation mode 1, other auxiliary operation modes 2 and 3 are provided.
What are also important are the scaling type settings.. Weighting should always be set to rotary weighting for spindles.
- S-0-0076 position scaling type (bit 2-0)
- S-0-0044 speed scaling type (bit 2-0)
- S-0-00160 acceleration scaling type (bit 2-0)
Parameter:
(000) unscaled
(001) translatory scaling
(010) rotary scaling
Notice
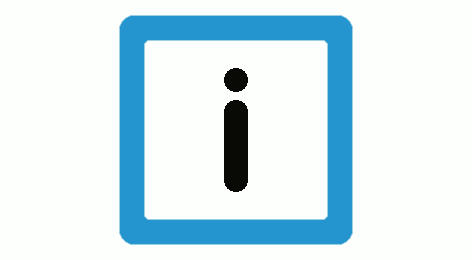
The operation mode for velocity control is specified for SERCOS drives in the parameter P-AXIS-00264.
Normally, this is the 1st auxiliary operation mode (antr.sercos.op_mode_for_velocity_control 1).
CANopen parameters
The objects below are essential for the position control operation mode with a CANopen drive:
Object 6060h (Modes of operation) = P-AXIS-00463
- Object 607Ah Target position
- Object 6064h Position actual value
After DS402 the following applies to Object 6060h in the position control operation mode by default:
Object 6060h = Cyclic_synchronous_position_mode_CSP(8)
After the changeover speed is exceeded, the CNC changes automatically to speed control.
Object 6060h (Modes of operation) = P-AXIS-00464
The following object is required for this operation mode:
- Object 60FFh Target velocity
- Object 606Ch Velocity actual value
After DS402 the following applies to Object 6060h in the speed control operation mode by default:
Object 6060h = Cyclic_synchronous_position_mode_CSP(9)
In addition, the CNC requires feedback from the drive regarding which operation mode is currently active.,
Object 6061h (Modes of operation display)
Notice
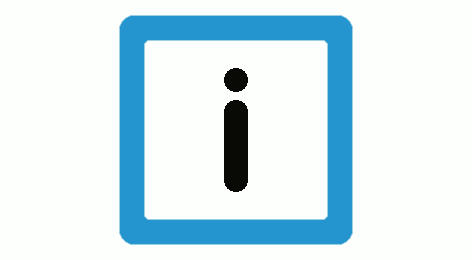
The operation modes for position and velocity control are specified for CANopen drives in the parameters P-AXIS-00463 and P-AXIS-00464. Normally, they refer to "Cyclic synchronous position mode" (8) and “Cyclic synchronous velocity mode“ (9).