KIN_TYP_12 – Tripod kinematics
Kinematic structure
The strut kinematic structure (referred to as “tripod”) consists of 3 translatory axes in a non-Cartesian arrangement. Strut pairs parallel to each other carry the tool holder platform. Tool orientation is constant.
Axis configuration in the NC channel | ||
Axis identifier | X, Y, Z (Z1, Z2, Z3) | |
Axis index | 0, 1, 2 | |
Kinematic structure | ||
| Tool axes | Workpiece axes |
NC axes | X, Y, Z | - |
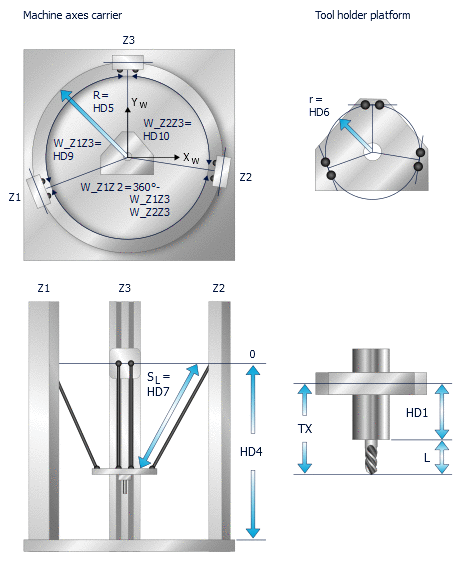
The parameter HD8 is used to toggle between an ideal (1) and non-ideal (0) tripod. An ideal tripod has an angle of 120° between all columns. A non-ideal tripod must be defined by the angles HD9 and HD10.
The third angle between columns is calculated as follows:
W_Z1Z2 = 360° - HD9 – HD10 = 360° - W_Z2Z3 – W_Z1Z3
Offset data of kinematics
HD offset | param[i] | Description | Unit |
HD1 | 0 | Tool offset Z | 1.0 E-4 mm |
HD2 | 1 | Tool offset Y | 1.0 E-4 mm |
HD3 | 2 | Tool offset X | 1.0 E-4 mm |
HD4 | 3 | Z axis offset machine origin | 1.0 E-4 mm |
HD5 | 4 | Radius to connecting line of the joint centre points on the drive columns (large circle) | 1.0 E-4 mm |
HD6 | 5 | Radius to connecting line of the joint centre points on the holder platform (small circle) | 1.0 E-4 mm |
HD7 | 6 | Strut length to each joint centre point | 1.0 E-4 mm |
HD8 | 7 | Switch to switch over to non-ideal tripod | [ - ] |
HD9 | 8 | Angle of column / joint 3 to column / joint 1 | 1.0 E-4° |
HD10 | 9 | Angle of column / joint 3 to column / joint 2 | 1.0 E-4° |