KIN_TYP_5 – 4-axis kinematics with crosshead for 4 tools
Kinematic structure
The kinematic structure consists of 3 translatory axes and 1 rotary axis in the tool.
Axis configuration in the NC channel | ||
Axis identifier | X, Y, Z, C | |
Axis index | 0, 1, 2, 3 | |
Kinematic structure | ||
| Tool axes | Workpiece axes |
NC axes | X, Y, Z, C | - |
The tool that is currently active is specified by assigning tool offset HD5 to the C axis. HD5 is calculated positively from the zero position of the C axis (Y axis) in the direction of the tool position.
If the 4 tools are arranged at right angles to each other as shown in the figure above, changing spindles results in a rotation of the C axis through 90° or 180° and translatory shifts of the X axis and Y axis. This is due to the geometry constants when RTCP is active.
Notice
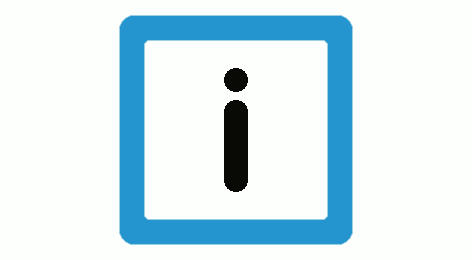
A data record containing head parameters must be kept for each head tool. The related tool head data record is used to select one of the tools 1 to 4.
To measure the head offsets of the individual tools, the related tool is rotated and brought to zero position of tool 1 (positive Y direction).
Besides the uniform head parameters HD1, HD4, HD5, head parameter HD2 is used for tools 1 and 2 and head parameter HD3 for tools 3 and 4.
Offset data of kinematics
HD offset | param[i] | Description | Unit |
HD1 | 0 | Offset tool holding device to reference point | 1.0 E-4 mm |
HD2 | 1 | Offset reference point rotation centre point C axis tool 1 and 2 | 1.0 E-4 mm |
HD3 | 2 | Offset reference point rotation centre point C axis tool 3 and 4 | 1.0 E-4 mm |
HD4 | 3 | Z axis offset tool holding device | 1.0 E-4 mm |
HD5 | 4 | Rotary angular offset C axis zero position | 1.0 E-4° |
HD7 | 6 | Static tool offset in X | 1.0 E-4 mm |
HD8 | 7 | Static tool offset in Y | 1.0 E-4 mm |