Test example with drive simulation
PLC test environment
Configuration of a Z axis according to CANopen DS402 drive with additional distance sensor (0x60E4_01).
Configuration of CAN drive
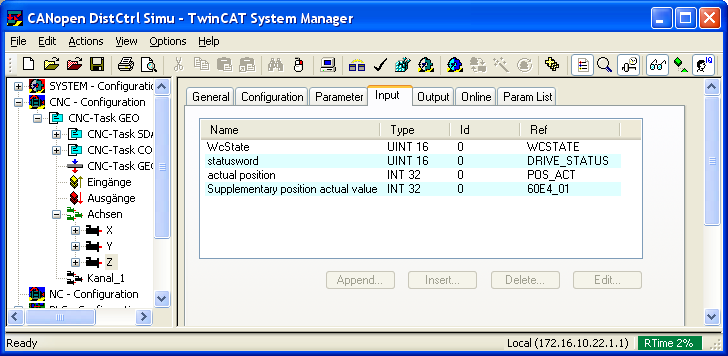
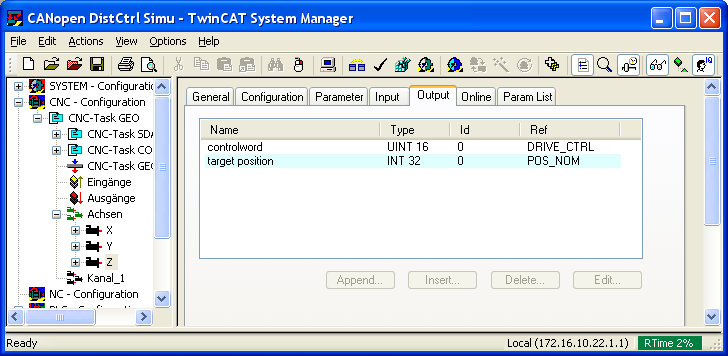
Simulation in PLC
Simulation of CAN-PDO via PLC inputs/outputs
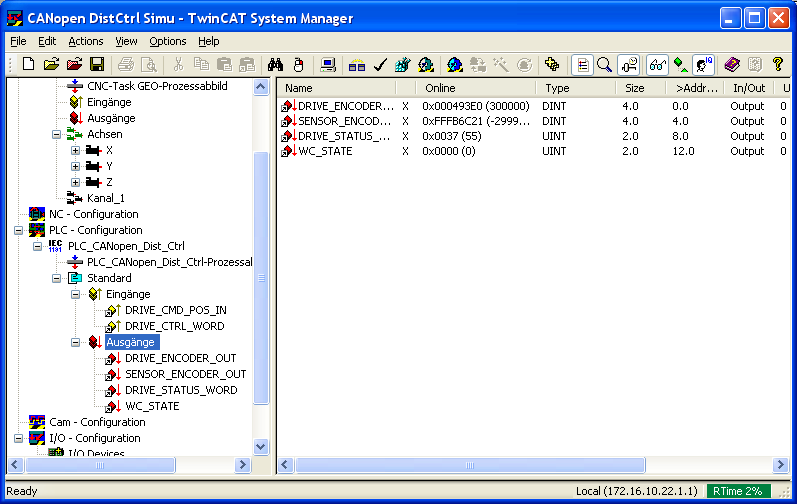
The drive encoder and the distance sensor are also subject to slight random noise.
Turning on the drives
The drive can be run after setting the drive enables (drive on, torque, feedhold off).
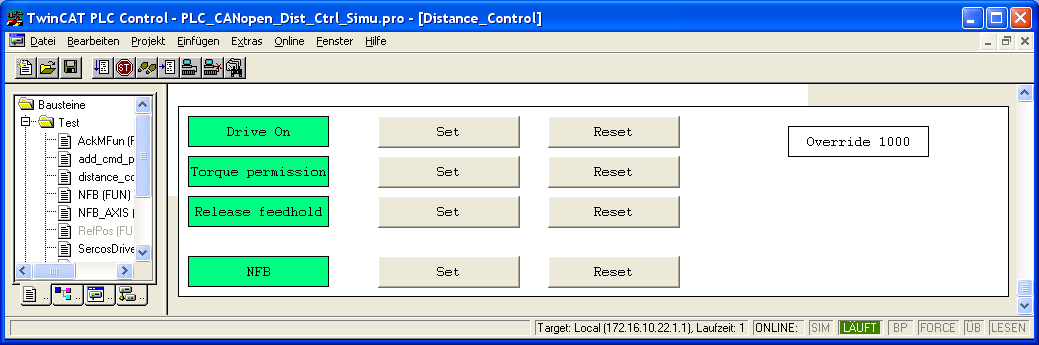
Approaching a set position
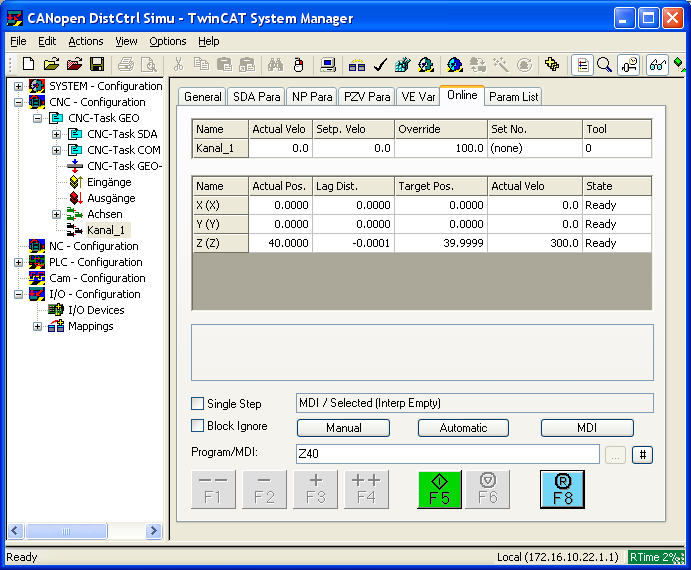
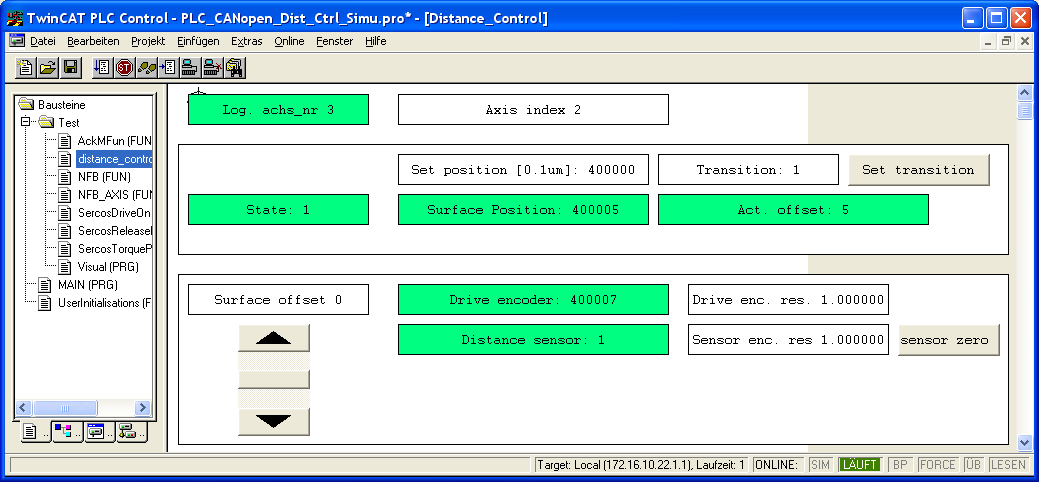
1. Referencing the sensor, “sensor zero”, 2. Entering the set position, 3. Position=400000, 4. Turning on distance control, 5. Transition=1 (ON)
In the transmitted set position (SET_POS) the distance sensor supplies the value = 0.
Changing the surface position “Surface offset”
The changed surface position results in a change in the measured distance sensor.
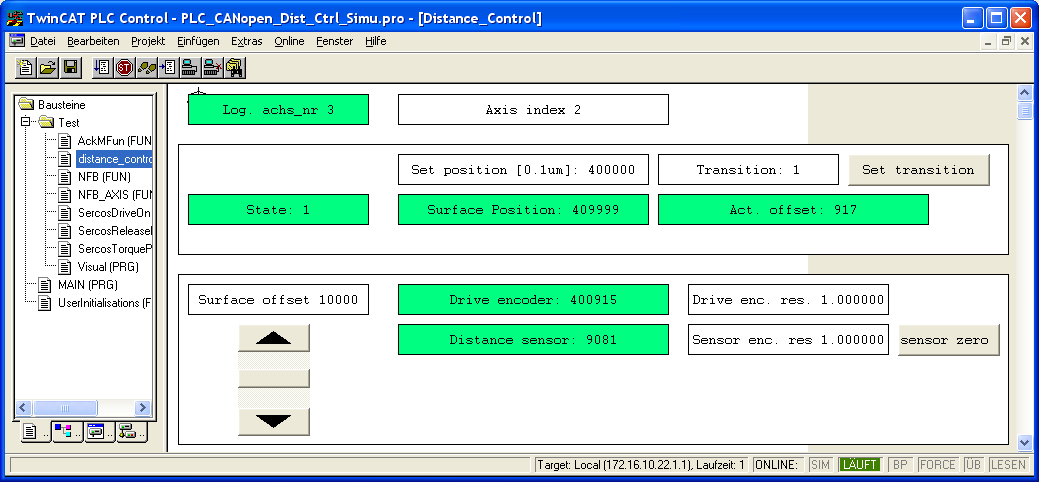
This causes a re-adjustment of the real axis position until the distance sensor supplies the value = 0 again. In other words the desired distance to surface is reached in this case.
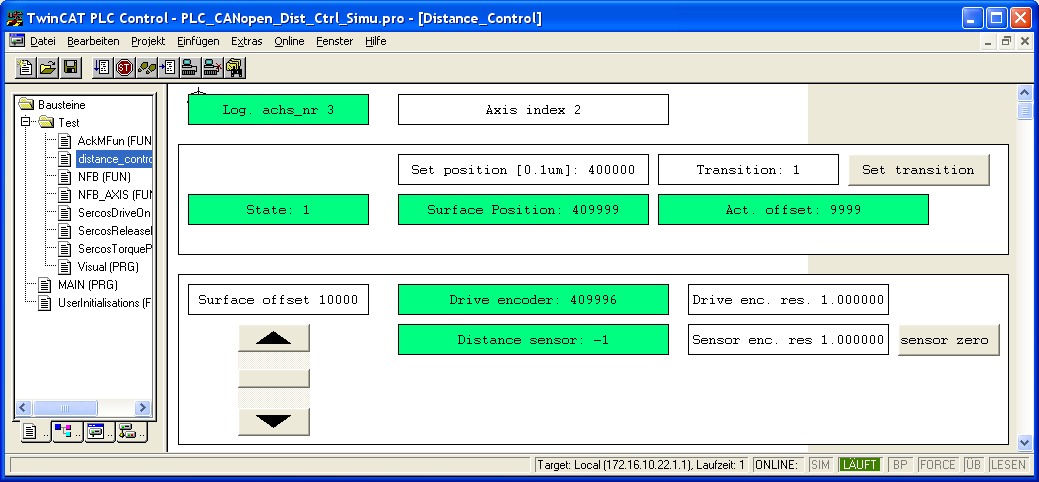
“Freezing” of the current height, transition=2 (FREEZE)
If distance control is interrupted (transition = FREEZE = 2), a changed sensor value (–20000) has no influence on axis correction in this time.
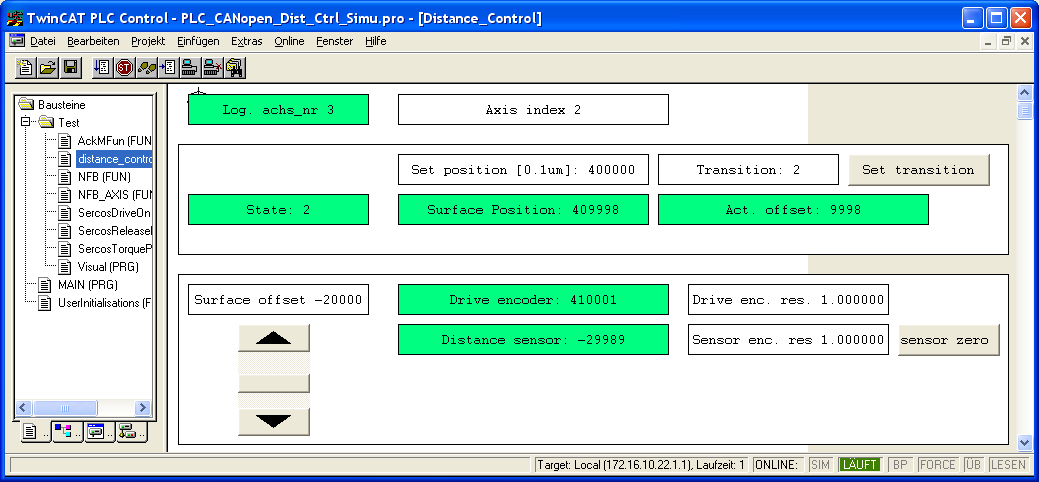
After re-activation of distance control the current sensor value is restored.
Turning off
Transition=0 (OFF)
After deselection of distance control (transition = OFF = 0) the position offset caused by the distance sensor is cancelled.